Resurfacing a 440 Chrysler
"RB" manifold to suit milled heads and
decked block at Wightman Engineering Services.
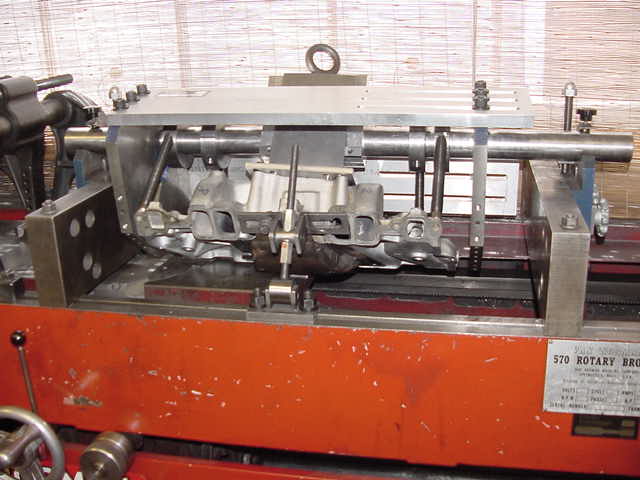
Re-cutting a weld repaired
vintage Corvette manifold for a
restoration job in an older Van Norman broach.
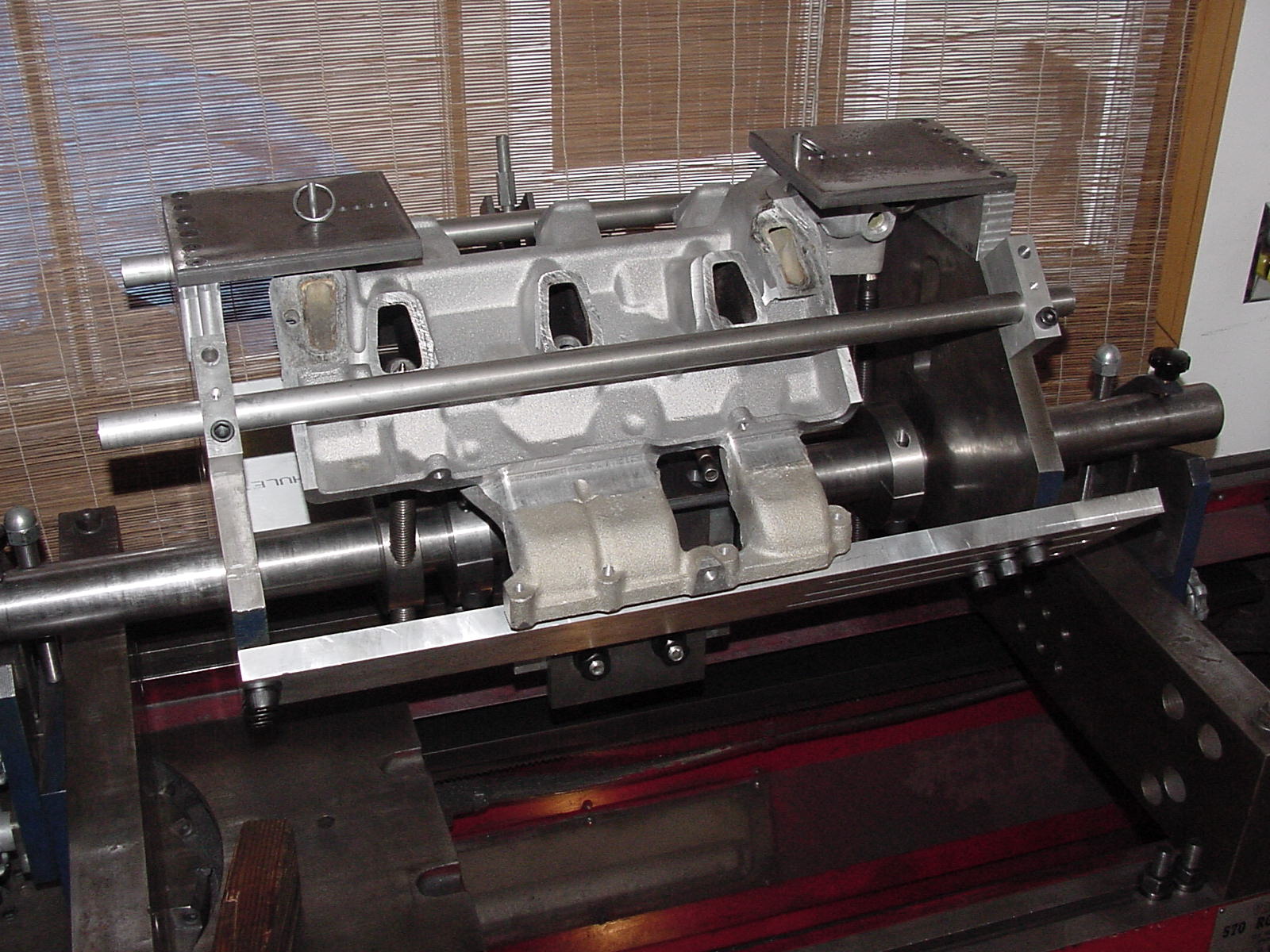
Aligning a late model 2.8
liter MPF Cadillac manifold prior to re-cutting
sealing surfaces for correction of vacuum and oil leaks.
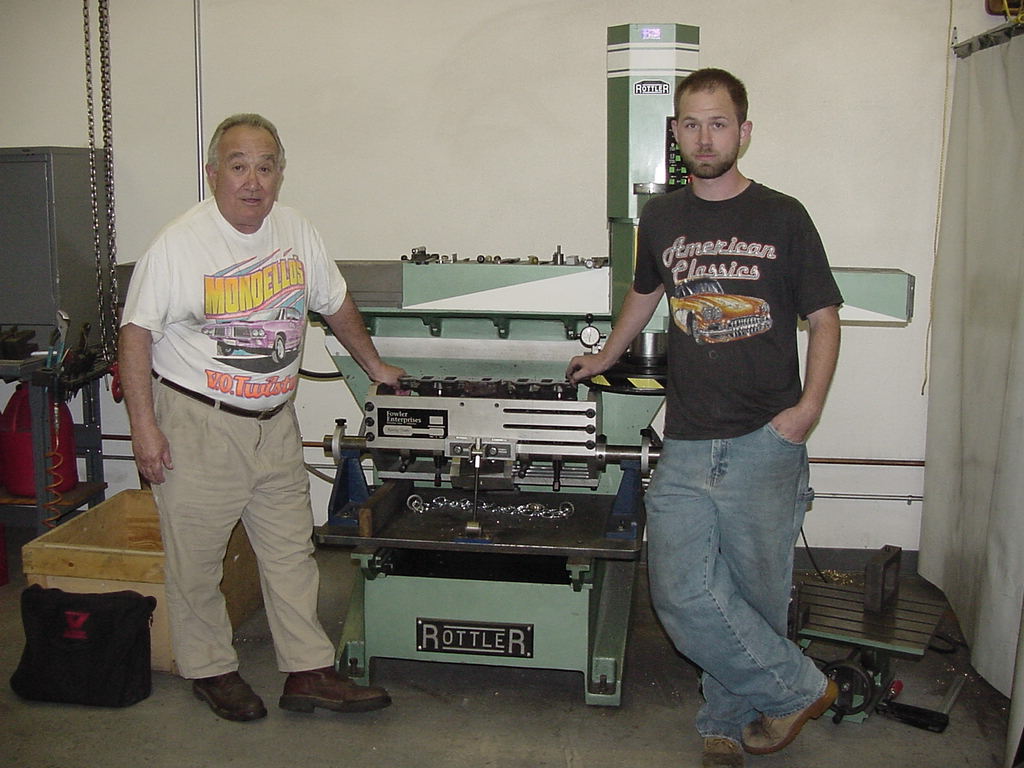
Joe
Mondello and his shop foreman
inspect a new fixture I installed in his Rottler surfacing machine for
the Mondello Technical School.
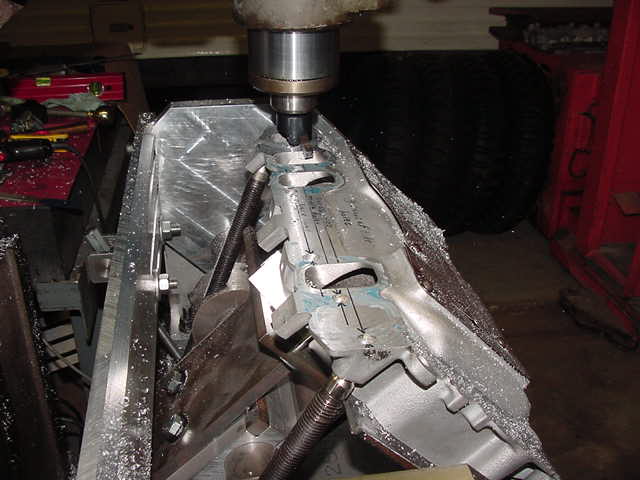
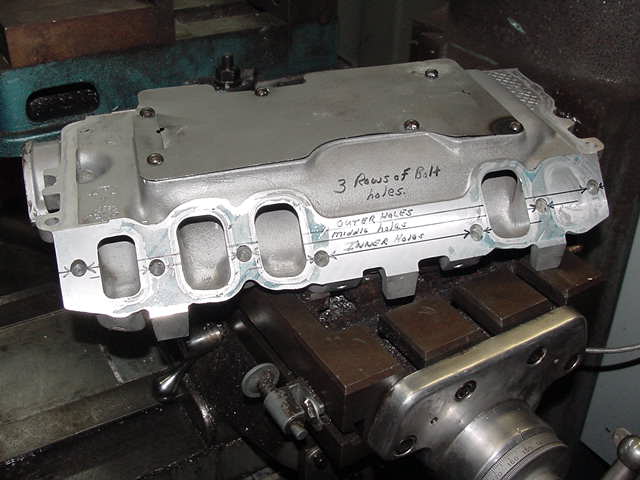
Ford
3.8 Supercharged manifold being
re-cut to suit a modified engine and checking bolt hole layout prior to
correction cuts at Fowler Automotive's shop in an older Bridgeport
clone mill.
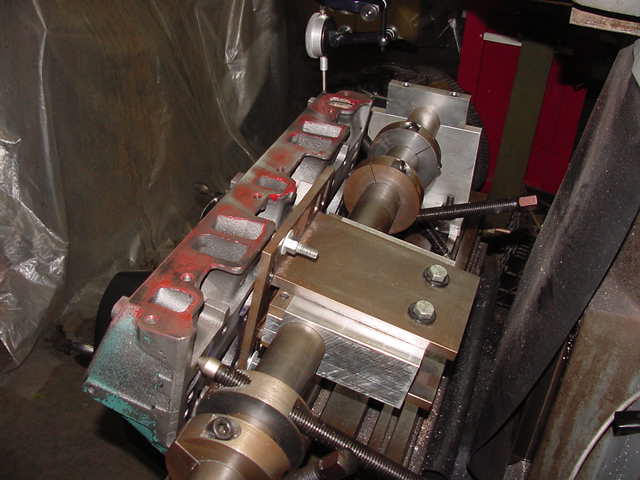
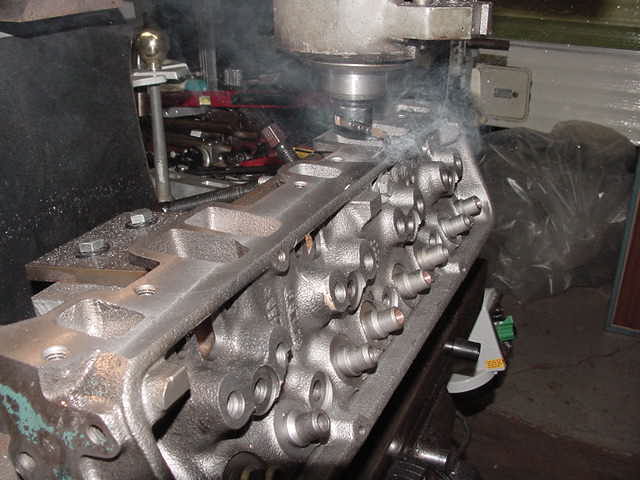
An
Intake Manifold Resurfacing Fixture
can be configured as a rollover fixture to recut the head side of a
sealing surface, then hold the head while being machined for screw in
studs and guide plates in one set up. This uses no additional parts or
jigs than those supplied with an original fixture purchase. When
combined with a BHJ torque plate secured between the head and fixture,
which has BHJ's precision located dowel pin option, production runs of
corrected and modified heads becomes very fast and accurate.
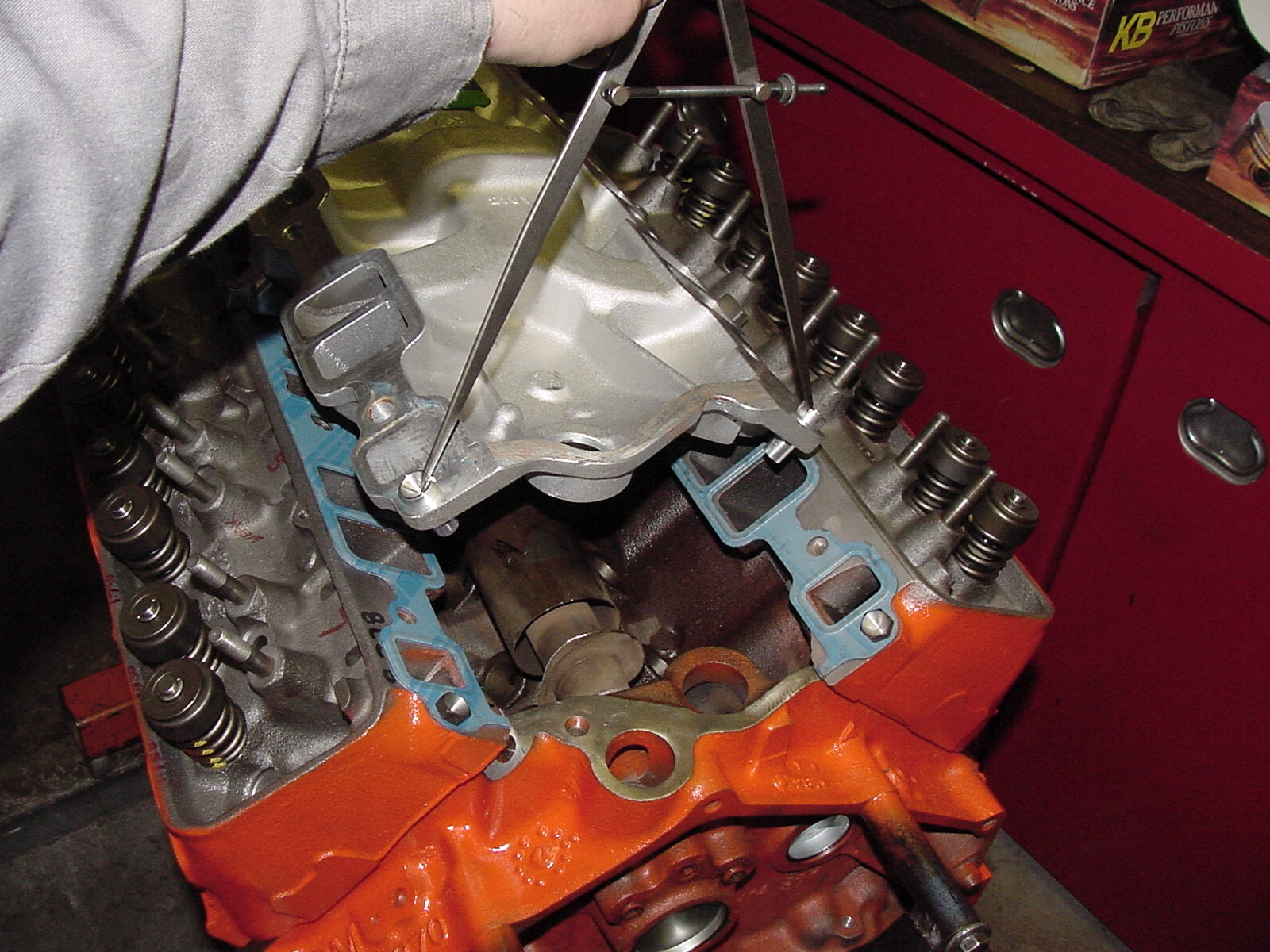
The
measuring jig and bolt system is very easy and accurate to use. It can
be
implemented when the manifold is still in the fixture so a job can be
checked at a midpoint to assure a good fit, or after machining for
quality control. It can be used just as effectively before a manifold
is worked on to pre-plan stock removal.
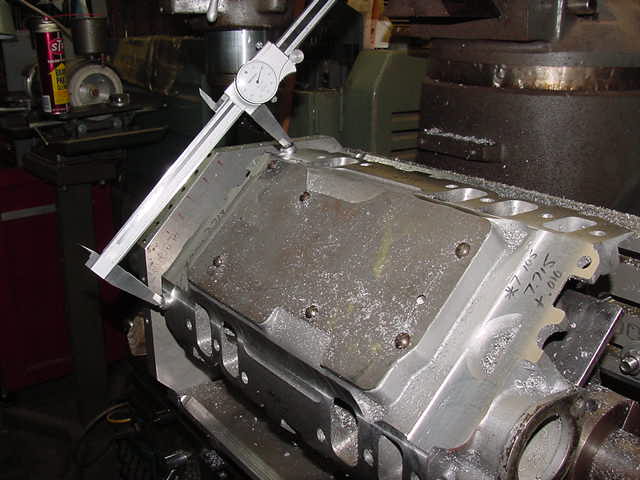
Back to Fowler Main
page